3D scanning and reverse engineering are transforming industries from manufacturing to healthcare. Michael Netherton placed himself at the forefronto ...
How Jinxbot Leads Zero-Waste 3D Printing
Written by: Carolyn Young
Carolyn Young is a business writer who focuses on entrepreneurial concepts and the business formation. She has over 25 years of experience in business roles, and has authored several entrepreneurship textbooks.
Published on January 14, 2025
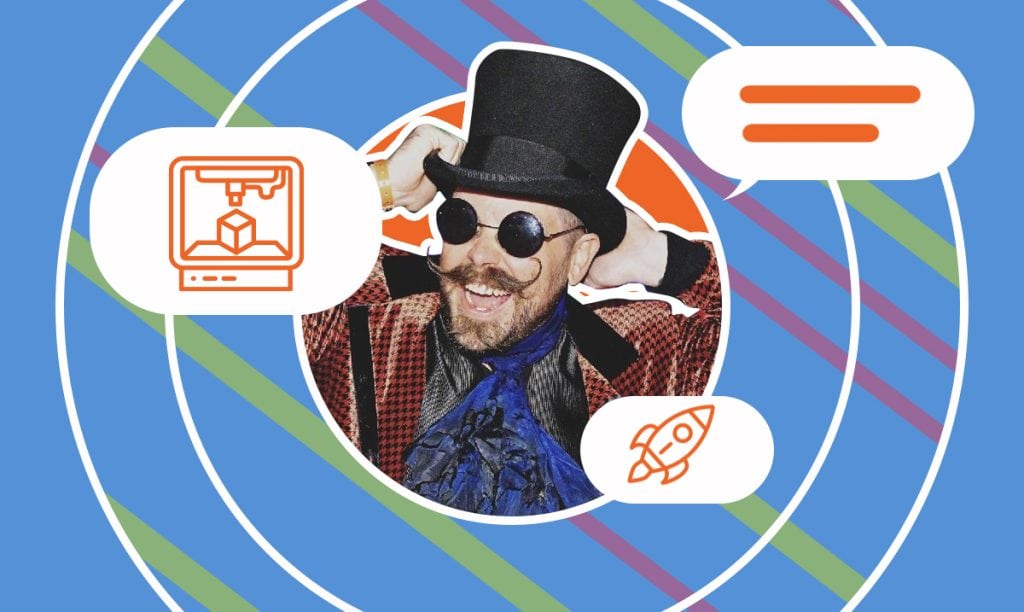
Jason Reynolds, founder of Jinxbot and co-founder of the zero-waste nonprofit PrintCycle, is leading the charge. With a passion for innovation and environmental responsibility, Jason has built a thriving business that not only pushes the boundaries of 3D printing but also sets a new standard for reducing waste in the industry. In this interview, he shares the story behind Jinxbot, the challenges of managing multiple locations, and his vision for the future of 3D printing.
The Origins of Jinxbot
SBS – How did you start Jinxbot 3D Printing?
Jason – There is quite a story to that. I went to Cal Poly in San Luis Obispo, where I studied industrial manufacturing engineering and then switched to industrial technology with a minor in packaging. My passion was always in ideation and business development — I wanted to be an inventor. Some of my projects during college were to create a product, market it, and do everything involved with product development and starting a business.
One of my first projects was called Puzzlers. It was a cute idea about vitamin-enriched gummy candies that could fit together. While developing that product, I got exposed to 3D printing when I needed to make prototypes for my candy molds. That was my second encounter with 3D printing — the first was around 2003 or 2004, during a design class in high school. My teacher just happened to know someone with a 3D printer (back in the day, those were very rare and expensive), so he 3D printed our designs. I saw magic when I held something I had created in 2D!
After college, I did sales (cars and electronic components) and software unrelated to 3D printing or manufacturing. During that time, my wife had a clothing business on eBay, thrifting and curating clothes and selling them in her online boutique. I also did email marketing for a solar electricity company called Sungevity. The industry tanked a bit, so the company let go of many employees, me included, though I didn’t feel bad about losing my job. At that time, my wife got a job at Stanford, so I didn’t have to say no to a paycheck, and we still had insurance. When we switched to her being the breadwinner, I asked her, “Hey, Amanda, can I try 3D printing for a living?” She said, “Okay, I’ll give you a year,” and she did. Without her support, I would not have been able to succeed.
That year, I built my business off a few online service bureaus where I listed my offers. I grew my business through that exposure, local word of mouth, and a lot of hard work and effort. At the end of the year, I was even making a profit!
At first, I had my printer at my desk at home. Then, I moved down to my garage and started filling it with printers. With that one printer, I earned enough to buy two, two to buy four, four to buy eight, eight to buy 16. Pretty soon, I reached the electrical capacity limit of my garage. Then, the pandemic hit.
The space I’m using now used to be a drop-off place for a laundromat down the street across from my house. They didn’t need a second location because everything shut down during the pandemic, so they went up for sale. I hopped on it, went through the change of use permit, and changed my business license from home to an established brick-and-mortar location. That was a nightmare. It almost didn’t happen a few times. They thought that I was a paper printing place and mislabeled me. They also thought I was doing manufacturing when I was just doing retail. There was a lot of working with the city closely during the pandemic, which was a huge challenge.
Still, I was able to eventually open my doors. I built a full-fledged print farm in Mountain View, California. Again, I established myself as a trustworthy local 3D printer. Since then, I’ve printed for Tesla, Google, Texas Instruments, and a number of different Bay Area-based companies. I just got onboarded as a preferred vendor for Apple and Meta.
This last year has been slow, but we now have two locations. The first one is more focused on the retail aspect and is more customer-facing. The second location is more of a laboratory with bigger industrial shelves and more printers. I’ve moved some of my larger printers over there, so that’s now the base of operations.
SBS – Do you now have people working for you, or are you still doing everything on your own?
Jason – I’m doing everything on my own. Solopreneur.
Balancing the Business
SBS – How are you juggling two locations by yourself?
Jason – I have been managing so far. At my remote location, I have optimized many things for remote presence. I can log in from my shop and start prints, maintenance, etc. Once a week, I go there to do some maintenance work. Once a day, I pop into the lab, pick up the finished parts, clean them up, and bring them back to the shop. In front of the shop, I have a kind of homebrew Amazon smart locker system where I can put items and give my customers temporary codes to pick up their orders whenever they like.
When it comes to customers, I still have to deal with them individually because their projects require that. You need to educate people through this process because many of them have never done it before.
I developed my own CRM system through Google App Sheets. That has been a wonderful tool to help me automate much of customer communications, and it lets customers know which stage of production their product is in.
I’ve tried to work with people before, but it hasn’t worked out. I think I’m looking for more of a partner than an employee because of how the business is and the attention the customers need. It’s been difficult to hire someone to do some ancillary work when I’ve already gone through the process of automating so much. Hiring someone doesn’t make sense for those roles, so I shot myself in the foot a little bit there.
Innovations and Expectations
SBS – What innovations have you seen in 3D printing, and what do you expect to advance in the future?
Jason – 3D printing went through a bit of a roller coaster itself. Initially, only large companies had access to this technology, which was under patent and protected. When some of those patents expired, the industry exploded, and the hobbyists started making their own machines that were smaller and more affordable. Unfortunately, the quality wasn’t there in the early stages of the industry. Then, the hype kind of died off. After that, there was a resurgence when more hobbyists joined, and the entire community was trying to build 3D printing. People were making home units, which were so reliable that the companies would start copying and further developing them. It started with Formlabs, MakerBot, and many of those older companies.
Now, the dominant players in the field are Creality, Bambu, and Carbon, though the latter two are a little bit more specialized for rapid manufacturing with highly specific materials. At Jinxbot, we use Creality printers specifically because they are easily repairable. The other machines are more on the Apple side — you need to send the entire machine back to the manufacturer for repairs, or they will refer you to specific replacement parts. Creality is great because it’s compatible with other brands’ parts. If you need to replace a fan, for example, you can get 10 of them for $10 off Amazon.
Next, magnetic build plates were an innovation that changed everything. 3D printers would have to scrape parts off of build plates and would get gashes in their hands in the process. I have quite a few scars in my hand because of that. With the advancements in manufacturing in general, people can make better and better 3D printers. The Creality K1 series is unbelievably reliable for what it is, and it’s extremely cheap. You can get a 220x220mm build plate volume printer that’s near the top of the line in this day and age for about $500. It’s an incredible way to get into the hobby without spending thousands of dollars on a quality machine.
There are also unbelievable things happening in slicer technology. Slicers turn 3D models into G-code, which is what the printer reads. Slicing technology has improved quite a bit, and it’s only getting better. I can only imagine what improvements AI will make in this technology in terms of optimizing the tool path for laying down the material and prolonging the life of your machine. Some 3D printers will understand what I’m talking about here, but if you’re moving fast back and forth between different points and geometries, that can have a lot of wear and tear on the motors and your machines, which will shorten the lifespan of your 3D printer.
With business in general, I’m excited for AI to help take over some of that administrative work. Maybe I will be able to clone myself with some AI, offering customers some basic knowledge and getting them in and through the sales process.
In this industry, people often leapfrog each other, coming up with different innovations. A lot of people are very interested in multicolor printing. As someone who has been professionally printing for the last decade, I’ve had very little need for multicolor printing. Usually, when I say that to people, they’re surprised. However, many people who are into printing figurines are also into the finishing work, so they don’t want or need the plastic to be different colors.
Some people are also interested in multi-material printing because they want to be able to print geometry that’s not optimized for printing (it has many overhangs or needs a special kind of internal geometry support). Support material is generally printed with the same material as the print. If you have an overhang, you can’t print over the air, so you’re printing on support material designed to be removed. Sometimes, people will print multi-material with a dissolvable filament. This allows them to print complex overhangs or internal geometries, then pour in water, acetone, or another chemical compound that’ll dissolve that support material and leave them with a nice finished part. Well, I would venture to say that that’s a poorly designed part in the first place. You can go back to the drawing board and redesign your part, so you do not need any support material. With relatively few design changes, you can readily transition any regular DFM part to design for additive manufacturing instead.
Standing Out
SBS – What makes you different from other 3D printers in your area?
Jason – There are a few main reasons. I’m located in the Bay Area, among many larger companies, and I can turn around parts in 48 to 72 hours. Also, I offer local pickup, and no online service bureau can beat that.
My customers send an order online. I print it within 48 to 72 hours and throw it in a locker for them to pick it up within a certain timeframe. If you go to a service bureau online, they must ship your item. It will take them two weeks to produce your order and 3–5 days for delivery, if not longer. When discussing development cycles, especially in the Bay area, that’s years and years, but people are now used to instant gratification. With engineers and their product development cycles, if they create an item and make a small change, they must test it to see whether it will work. Being able to turn that around quickly is a huge benefit compared to waiting for two weeks or more and possibly repeating the process a few times until you get a perfect product.
Some people will buy a 3D printer to solve those development times. That’s a great solution if you have someone in your team dedicated to running it. However, many smaller businesses will make the mistake of buying a 3D printer without realizing how much time, dedication, and effort it takes to make those 3D-printed parts quickly. You need to know how to repair the machine. You need to learn the slicing software. You need to know what works and what doesn’t work for 3D printing… If you don’t have someone with the experience to identify those issues, then you’ll be spending a lot of time, almost the same amount, that it would take you to send your design off to one of those online service bureaus.
Another reason why Jinxbot is different from many other printing places is customer service. With some other places, you need to go online, submit your file, and hope your design can be printed. You could be waiting for two weeks or more only to get a part with something missing or with something that wasn’t supposed to be there. If there is no consultation process, you won’t get any feedback. When you submit an order to Jinxbot, we review the part file and try to understand your end goal. We can suggest adding more strength, accuracy, or another material that would be better for your end-use case.
Jinxbot is a registered zero-waste business. Since 3D printing is a wasteful industry, we have started a nonprofit called PrintCycle that takes in 3D-printed scrap material. We’ve been working with Stanford, Berkeley, Hacker Dojo, and Maker Nexus on reclaiming their 3D-printed scrap material, chopping it up, and using that for injection molding to make other useful goods. I’ve also done the same with my scrap material. We also reduce the amount of scrap material by printing correctly the first time. We also use all recycled packaging and have local pickups, which reduces packaging even more.
Material Favorites
SBS – What are some of your favorite materials that you work with?
Jason – I’ve been a fan of PLA for quite a while. Back when 3D printing was getting off the ground, there were two primary competing materials — PLA (polylactic acid) and ABS (acrylonitrile butadiene styrene).
ABS was always touted to be a more robust material. It is also UV-resistant. Unfortunately, it’s a very toxic substance, and when it melts, it smells and leaves films on glass windows. People have also developed respiratory issues due to this chemical. It’s also not biodegradable.
Though I was always more of a proponent of PLA, it is a harder material, which makes it a little bit more brittle. PLA wasn’t preferred for products that needed to be durable or field-tested. However, as the industry kept evolving, people realized that PLA could be doped with different materials to be less brittle, more durable, and easier to print with. PLA also doesn’t off-gas as much as ABS does (ABS emits gas in the parts per million, while the PLA gas emissions are in the parts per billion). PLA barely has any smell. If it has, it’s a bit sweet since it’s a sugar-based plastic. Engineers have doped PLA with carbon fiber, wood, or metal. You can get a metal-filled PLA that will rust (for example, if you’re making a metal figurine that needs to look aged).
Many other FDM materials exist, like ASA (acrylonitrile styrene acrylate) and TPU (thermoplastic polyurethane). TPU is a flexible material. ASA is a cousin of ABS, but it’s a little easier to work with, it’s not so toxic, and it’s even more UV-resistant.
Talking about materials in general, I’m a huge fan of our SLS (selective laser sintering), which utilizes nylon 11. It’s an incredible biocompatible material that doesn’t require any support material. We’ve made some highly durable prosthetic limbs out of this. If you give it any thickness, it becomes very strong and dense. As I said, removing support material from the equation makes it great to work with. You get great surface finishes on every side and can take advantage of the entire printer volume. For regular FDM printing, you must use your build plate, a 2D space, to place your 3D items on, and there’s only so much you can fit on it. With SLS, you can stack things on top of each other because it’s a powder-based material. The powder base is in this kind of cylinder, for lack of a better word, and the powder on top of it creates its support material. When you take your print out of that powder, you just need to dust it off, and your object is done.
Advice for Future 3D Printers
SBS – What advice would you give fellow enthusiasts who want to start a similar business?
Jason – I’ve always been a proponent of slow but steady wins the race. When I started, it was with one machine. That was a really good test to see if this was something that I wanted to do. Printing for yourself is one thing — you’re your only client, you have all the time in the world, and if your print fails and you need to print it again, there’s no deadline, so it’s no problem. When you start printing for another person, and they have a timeline, then the pressure’s on, so your prints need to work.
Also, throw a quick website together through WooCommerce, Squarespace, or another platform. It’s very easy to do these days. I recommend doing that rather than joining one of the service bureaus. 3D Hubs used to be a wonderful website, but in terms of the quality and the way they treat their printers, it has fallen off an incredible amount in the last few years. So, start your website, get a plug-in, get some auto quota, and then take on clients one at a time. Etsy is a great place to start for that as well.
I provide a general print-for-hire type of service, which is not what many people would like to do. That is difficult because you’re dealing with many different education levels and some potentially very frustrating people. Most people would choose the other route. They might have an idea for a product and will print it as they get orders through Etsy, their website, or another platform. Although that’s a great way to go about it, it can be a bit slow-going and is very product-dependent.
Since I work with larger and smaller companies and everyone in between, I often get calls from people who have never 3D printed before. They need me to walk them through this process, so I have to be very patient. I love and am very passionate about 3D printing in general, so if someone comes to me and asks if they should buy a printer to print something more expensive, I always advise them to do it. I want them to have this superpower! That said, not everybody’s willing to do that, and that’s why Kinko’s still exists.
Subscribe to Our Newsletter
and gain insider access to cutting-edge business insights and trends.
Featured Resources
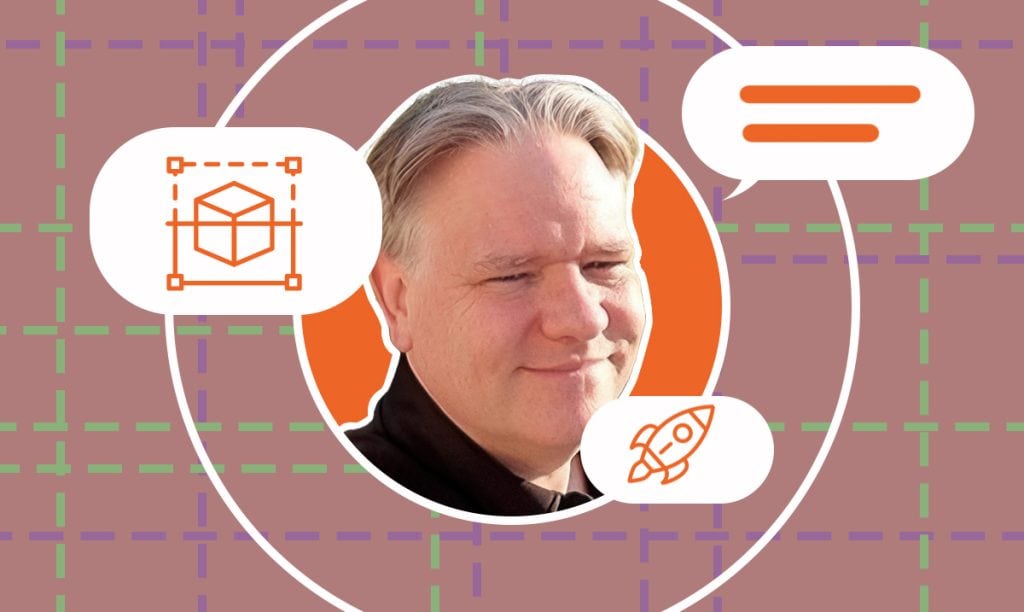
How 3D Scan STL Revolutionizes Reverse Engineering
Published on January 2, 2025
Read Now
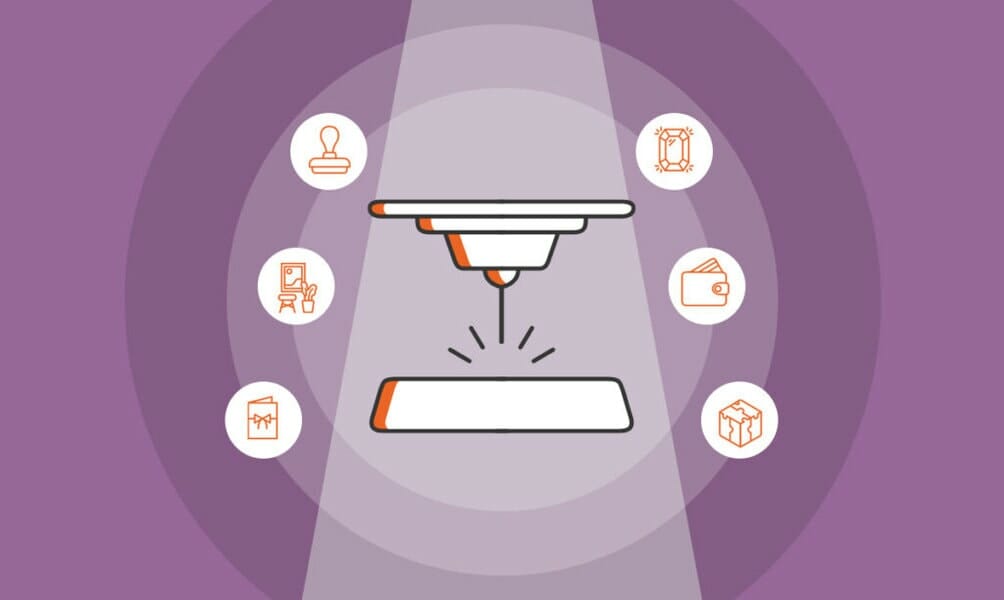
15 Glowforge Business Ideas – Make Money with Glowforge
Published on December 21, 2022
Thinking of turning your crafting talent into a business? A Glowforge 3D Laser Printer can produce valuable goods and big profits with its precisecu ...
Read Now
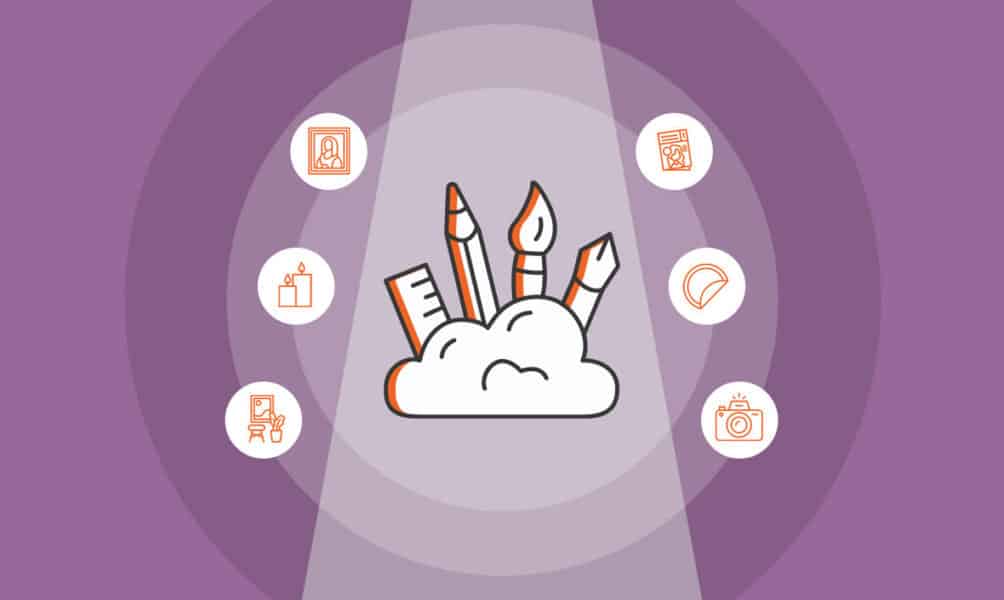
38 Creative Small Business Ideas to Inspire You
Published on June 30, 2022
Want to express your creativity and be your own boss? There are many creative business ideas out there that can help you check both boxes, and makeg ...
Read Now
Comments